Housing
The heater’s case or housing can be manufactured using aluminized steel or stainless steel. Additionally, in some cases the heater can be supplied without a case.
Aluminized steel is the most commonly used case material. It can achieve very high temperatures — namely 1200°F (649°C) — without flaking, discoloring, or degrading; this assures that the heater’s case will outlive the heater itself. The housing is typically riveted together. The rivets, along with slots in the heater case, permit controlled expansion and contraction during heat-up and cool-down processes. Some applications require the slots to be removed, which can be achieved for many engineering designs.
Stainless steel’s advantages of enhanced cleanliness and a very polished appearance make it a good choice for food and semiconductor applications. Because the 304 grade of stainless steel will discolor at a lower temperature than aluminized steel, the 310 grade of stainless steel is often chosen for extremely high temperature applications. A stainless steel case is usually riveted together in the same manner as aluminized steel though there are some applications where the stainless case is welded and polished for superior cleanliness and cosmetic appeal. Additionally, those housings are usually supplied without expansion slots. This construction is typically implemented in our glass, koramic and quartz face heaters.
The last option, called board only, is to have no case at all for the heater. This heater is usually an F-Series model without the housing, insulation or pre-constructed panel design. Customers who have in-house sheet metal capability will sometimes choose to buy the heating element, fiber board, quartz fabric and cement as a completed assembly. The remaining components of the panel fall under the customer’s responsibility. This approach shifts much of the heater’s construction and warranty issues toward the customer.
Standard Dimensions
Width (mm) | Length (mm) | F | FBA | G | K | M | Q |
6″ (152.4) | 12″ (304.8) | 18″ (457.2) | 24″ (609.6) | 30″ (762) | 36″ (914.4) | X | X | X | X | X |
|
6″ (152.4) | 42″ (1066.8) | 48″ (1219.2) | 54″ (1371.6) | 60″ (1524) |
| X | X |
| X | X |
|
10″ (254) | 4″ (101.6) | 6″ (152.4) | 8″ (203.2) | 10″ (254) |
|
|
|
|
|
| X |
12″ (304.8) | 6″ (152.4) | 10″ (254) | 12″ (304.8) |
|
|
|
|
|
|
| X |
12″ (304.8) | 12″ (304.8) | 18″ (457.2) | 24″ (609.6) | 30″ (762) | 36″ (914.4) | X | X | X | X | X |
|
12″ (304.8) | 42″ (1066.8) | 48″ (1219.2) | 54″ (1371.6) | 60″ (1524) |
| X | X |
| X | 42″ or 48″ |
|
12″ (304.8) | 72″ (1828.8) | 84″ (2133.6) |
|
|
| X | 72″ only |
|
|
|
|
16″ (406.4) | 16″ (406.4) | 24″ (609.6) |
|
|
| X | X | X | X | X |
|
18″ (457.2) | 18″ (457.2) |
|
|
|
| X | X | X | X | X |
|
24″ (609.6) | 24″ (609.6) |
|
|
|
| X | X |
|
|
|
|
Note: Solar Products specializes in manufacturing custom heaters that match a specific application. Listed above are standard heater dimensions.
Voltage
Because Solar Products is a custom manufacturer of heaters, we can design our heater models for all commercially or industrially supplied voltages including 120, 208, 220, 230, 240, 277, 380, 415, 460, 480, 575 and 600. In many cases, our heaters are provided with dual voltage to help reduce heater stocking requirements. Dual voltage heaters accept a derivative of two voltages, usually 120/240 or 240/480. Three voltages can be provided for heaters with a minimum of six heating elements and seven terminals. This wiring arrangement can be configured for three voltages and dual phase.
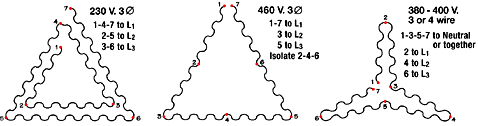
Phase
Solar Products can manufacture our heaters for single, three or, in some instances, dual phase.
Frequency
Because fixed resistance heaters operate using any particular frequency without requiring design changes, frequency is not a significant issue.
Fixed Resistance
Our heaters are all fixed resistance. This means that the wattage attained is a direct result of the voltage applied (W= V2/R). In other words, if the voltage varies the heater wattage will vary by a squared relationship of the voltage unless the heater is properly controlled. Proper control makes use of a temperature controller or a power controller that can maintain a constant power output. Solar Products’ heaters are designed for hot resistance to ensure true power output.
Zoning
The heaters can be separated into multiple zones in one given panel. An example is the use of three 12″ x 24″ (305 mm x 610 mm) zones in a 12″ x 72″ (305 mm x 1829 mm) heater or two 6″ x 48″ (152.4 mm x 1219 mm) zones in a 12″ x 48″ (309 mm x 1219 mm) heater.
This particular heater is divided in this fashion to accommodate different widths in a web application. Sometimes a heater is divided into an outer zone and an inner zone. A last option is to apply multiple oddly shaped zones to match a specific heating profile.
Edge Compensation
Another option that is applied to our infrared heaters is the use of edge compensation. This approach places a slightly higher watt density along one long edge of a heater (ex. a 24″ x 36″ 610mm x 915mm heater). To help compensate for heat loss along that open edge, a higher watt density is constructed into the heater’s design to reduce edge heat loss.
Depth
There is no standard thickness for Solar Products’ heaters. The most common depth is 3″ (76 mm). Our heaters can be manufactured as thin as 1.250″ (32 mm) and as thick as 6″ (152 mm). The heater depth is most often determined by available space and/or a required back temperature.
Wavelength
The wavelength output from our heaters ranges from 2.3 microns to 6 microns and is inversely proportional to heater temperature; that is to say, as the temperature increases the wavelength decreases. All heaters output energy over a range of wavelengths as depicted in the heater output curves appearing below.
Heater ‘A’ displays a typical shortwave heater, Heater ‘B’ displays a typical medium-wave heater, and Heater ‘C’ displays a typical long-wave heater. All of the curves have one common characteristic. If a line were drawn vertically through the peak of the curve, then the area left of the line represents 25% of the total energy output shorter than the peak wavelength, and the area to the right of the curve represents 75% of the energy at a longer wavelength than the peak.
Solar Products’ panel heaters output the majority of their energy in the medium wavelengths when operating at high watt densities and temperatures. When the temperature is reduced below 900°F (482°C), the majority of the energy falls into the longer wavelengths. The medium wavelength ranges from 2-4 microns, and the long wavelength ranges from 4-1000 microns. The effective process heating range for long wavelength infrared is from 4-6 microns. Six microns relates to a temperature of 500°F (260°C). An infrared heater with a surface temperature below 500°F (260°C) has little use in industrial process heating applications.
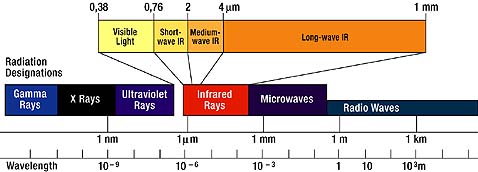
Complete Heater Layout
The heater below displays examples of the options that can be customized for our heaters and the typical positioning of heater components. All options, however, will not be used simultaneously on a production heater.
A – Snap-in Mounting Nut
B – 4″x 4″ Electrical Box
C – Information Tag
D – Compression Nut
E – Heater end
F – Back Mount Thermowell and Thermocouple
G – Bayonet Style Thermowell
H – Pyrometer Hole
I – Mounting Studs
Studs
Mounting weld studs are commonly located on the back of the heater near each corner. As a heater’s length exceeds 36″, stud(s) are added in its center. This is Solar Products preferred mounting option.The mounting studs size options are as follows:
Width | Length | | | |
1/4″ x 20″ | 1/2″ | 3/4″ | 1″ | 1-1/4″ |
8mm | | | 25mm | |
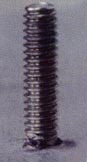
Mounting Stud
Nuts
Mounting nuts are commonly located on the back of the heater near each corner. As a heater’s length exceeds 36″, nut(s) are added in its center. The mounting nut size options are as follows:
Description | Available Nut Sizes | | |
Snap-in Nut | 1/4″x20″ | 5/16″x18″ | 3/8″x16″ |
Compression Nut | 1/4″x20″ | 5/16″x18″ | 3/8″x16″ |

Snap in Nut

Compression
End Pieces
One last mounting option is to use special metal clips or brackets on the ends of the heater in lieu of the studs or nuts. This approach can simplify the heater installation for certain applications.
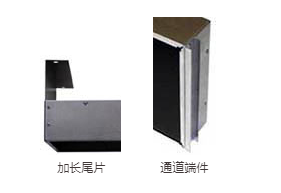
Thermowells are not required for our heaters. The heaters are sometimes controlled with percentage timing devices that switch them on and off based on a time cycle and optical thermometers. The temperature sensitivity of the application dictates the need for a closed loop, making use of a temperature controller and a temperature sensing device, or an open loop, not making use of a temperature sensing device and commonly operating on a percentage on/off basis.
End Mount Thermowell/Thermocouple
An end mount thermowell is the most common design. The thermowell is either a quartz tube (most common because of faster response) or ceramic tube located parallel to the heating element. The tube is typically 5″ (127mm) long and has an inner diameter of 0.157″ (4 mm). A thermocouple bracket is mounted outside the thermowell tube to assist in proper positioning and holding the thermocouple in place. The thermocouple is then located 4″ into the thermowell and fastened using the bracket. It is important to assure that the thermocouple is not over extended into the thermowell, which may result in incorrect temperature readings or heater failure. A thermocouple with a male plug is displayed.
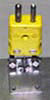
Back Mount Thermowell/Thermocouple
The back mount design makes use of an L-shaped quartz tube that runs perpendicular to the coil toward the back of the heater. The thermowell then makes an arced 90° bend, continuing for a short distance parallel to the heating element. This design is used when the heaters are surrounded, not allowing side access, and requires the use of a .040″ (1 mm) diameter thermocouple in order to make the 90° bend. A thermocouple with a male/female plug combination is displayed. This design is not available for the Q-Series.
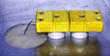
Bayonet Style Thermowell
The bayonet style thermowell is sometimes used with metal, koramic, glass and quartz face heaters to measure the actual face temperature (emitting surface) as opposed to the heating element temperature. The thermocouple goes through a bayonet fitting and is compressed using a stainless steel spring. This approach assures that the tip of the thermocouple makes correct contact with the heater face.

Pyrometer Hole
It is becoming more common for equipment manufacturers and end users to make use of optical pyrometers, or non-contact thermometers, to sense product temperature as opposed to heater temperature. In virtually all applications, product temperature is the temperature of choice. Heater temperature is only used as a reference in order to attain a particular product temperature. The reduced price for these devices and the quest for better process control has driven the use of optical pyrometers. For that reason, it is sometimes necessary to provide an opening (1.5″ – 2″ (38 – 51 mm) diameter hole) through the heater where the optical pyrometer can be placed to monitor the product temperature. The pyrometer hole size can vary based on the specific requirements. A smaller hole is always preferred to avoid nonuniform heating of the product.

Warranty
Solar Products’ panel heaters are covered by a one-year warranty against manufacturing defects.
Flag Type
The flag type terminal consists of a flat piece of stainless steel that is .350″ (8.9mm) wide x .032″ (0.81mm) thick with a .187″ (4.75mm) hole near the end. This is our preferred termination because of the excellent electrical contact that is achieved with this type of connection. All of the electrical terminal options are typically housed within a 2″ x 4″ (51mm x 101.6 mm) or 4″ x 4″ (101.6 mm x 101.6 mm) electrical box.

Stud Type No. 1
The stud type terminal consists of a threaded stud that exits the heater for an electrical connection. A number of different connection lengths and stud sizes are available. The disadvantage of a stud type terminal is the electrical current limit of the stud. An electrical current is only carried on the threads of the stud.
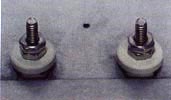
Stud Type No. 2
Another version of this connection is the ceramic block flag type terminal. This design makes use of a flag type terminal exiting the heater that is bent over a ceramic mounting block with a vertically mounted stud. This approach uses the stud as a means of easy connection but not as a current-carrying device. Therefore, higher current can be carried through the electrical connection. This type of connection is not available on all heaters.
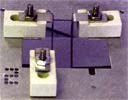
Wire Leads
Wire leads is a fourth termination option available on Solar Products’ heaters. This option is only available on heaters having a watt density lower than 10 watts per square inch (15.5 kW/m2). A high-temperature wire is resistance welded to an intermediate piece of stainless steel, and the steel piece is in turn resistance welded to the heating element. The wire leads can be fabricated in any required length.
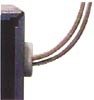